Entrained Gas Tester Manual
The Qualitest Advanced Air Entrainment Meter is used to measure the air content of freshly mixed mortar in accordance with the air pressure compensation principle. The Air Entrainment Meter has a pressure chamber in which a predefined pressure is generated.
When the overflow valve is opened, the pressure is compensated with respect to the test pot, which is filled with the freshly mixed mortar. The pressure drop is measured to give the air content in the mortar.Air entrainment is the intentional creation of air bubbles in concrete or mortar.
Excess water is often trapped within the mix as it hardens. The excess water eventually evaporates and leaves behind porous cavities. These pores create weaknesses in the concrete or mortar during freeze-thaw cycles. An air entrainment meter is used to measure the amount of air that is trapped within the mix. The sleek design of each of these units allow for easy storage on top of any workstation.Qualitest offers Air Entrainment meters in different capacities adhering to DIN EN 459-2; DIN EN413-2; ASTM C 185 and other international standards.
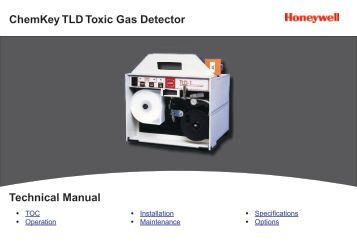
These meters are either with a sturdy hand-operated pump or with an electrical mini compressor for rapid and uniform provision of pressure.QUALIAEM-A1M Automatic Air Entrainment Meter 1L was designed to be efficient and easy to use for mortars. The built-in miniature air compressor is the perfect upgrade from the traditional manual pumps. This design also ensures that the operator doesn’t require extensive training or technical expertise. The large central meter ensures that the results and reading can be done effectively, easily and without strain.
The automated process also allows for great time savings and efficiencies in that it frees up the operator to attend to other tasksQUALIAEM-A8 & QualiAEM-M8 Air Entrainment Meter was designed to be efficient and easy to use. The built-in miniature air compressor is the perfect upgrade from the traditional manual pumps. This design also ensures that the operator doesn’t require extensive training or technical expertise. The large central meter ensures that the results and reading can be done effectively, easily and without strain.The automated process also allows for great time savings and efficiencies in that it frees up the operator to attend to other tasks with the QUALIAEM-A8.The manual Air Entrainment Meter design model QUALIAEM-M8 takes the best of the traditional machine and infuses it with a more modern look. It is the same, tried and true operation but with a sleek vessel and sturdy construction. Both units are built to last and would become the new work horses of your testing equipment. Another manual Air Entrainment Meter design is the QUALIAEM-M8I model for Concrete.
Features of the Air Entrainment Meter. Extreme sturdiness. Simple operation.
Great accuracy. Designed for ease of service. Pressure gauge with Class 1.0 accuracyThe Air Entrainment Meter is made of cast aluminum; locking bolts with palm grip give the test pot and upper section an airtight seal. Two ball cocks are provided to fill the required water and to vent the air. The air is compressed by means of a built-in hand pump.
The connection valve for the initial pressure and the overflow valve are integrated into the pressure chamber. The connection valve is a sensitive needle valve with a knurled head screw. The over flow valve for the pressure compensation between the pressure chamber and the test pot is operated by means of a valve rocker. The pressure valve is installed directly on the pressure chamber and the scale shows readings with a range of 0-100 vol%.
Foam & Entrained Air (Troubleshooting Guide)Foam(Entrained air, Visible foam)Air that is present in papermakingstock or can cause variouskinds of problems, including, circularmarks on the paper, reduced, unsightlyfoam, related to foam buildup, andloss of solid material due to overflow of foam from tanks and chests.The three main classes ofair that are of concern to papermakers are dissolved air, entrained air, andlarge bubbles. Dissolved air behaves as part of the water phase, except thatit can come out of solution as tiny bubbles (entrained air) if the pressureis reduced. Entrained air consists of bubbles that are small enough (say lessthan 1 mm) to move along with the fibers. Large bubbles have sufficient buoyancyto rise to the surface; however they still can be a problem if the bubbles arepersistent and build up as visible foam or froth.Though our main concernin this website is in regards to chemical factors, it is important to considermechanical factors that can be contributing to air problems.
Leaky seals onpumps are a leading cause of unnecessary air entrainment. Also it is importantto realize that the paper machine environment contains all of the key elementsneeded to create foam - water, air, lots of agitation and splashing, and varioussubstances that can act as stabilizers. On a basic, traditional paper machinethe main mechanism of air release is the coalescence, creaming, and breakageof bubbles in the and areas, just after the paper has been formed.
Often the breakageof surface foam is promoted by spray showers. It is important also to make surethat the showers within air-paddedare working effectively. Many modern paper machines, especially those producingfine and specialty paper grades, contain deaerating equipment. These involveapplication of vacuum and some type of fluid motion to separate dissolved andentrained air from the water phase.The most common short-termsolution to air problems is to add a chemicalproduct.
A wide variety of chemical formulations has been found to be effectiveto promote coalescence of air bubbles within papermaking stock and white wateror to break bubbles at the surface of water. Some common ingredients of theseformulations include water-insoluble,oils, water, and hydrophobic particles. An essential feature is that the liquidphase has to have a low viscosity and a tendency to spread rapidly on bubblesurfaces.
Different defoamer products may be needed in different paper machineenvironments. In particular, many defoamers have an optimum temperature range.Over-use of defoamers should be avoided due to cost and in order to minimizedeposit problems. Defoamers often are added in dilute solution either at a, just before,and as surface sprays.A long-term answer to airproblems in a paper mill also should include consideration of chemical factorsthat tend to stabilize foams. Sometimes these factors can be minimized. Surfaceactive materials tend to stabilize foams by lowering the interfacial tensionbetween water and air.
Likely sources of materials include, black-liquorcarryover (in unbleached kraft operations), excessive or saponified,and in the formulations of various wet-end additives, including some.Water-soluble, high-molecular-mass polymers such as and can be expectedto stabilize foam bubbles if the additives are used at levels beyond what canbe efficiently retained on the fiber surfaces. Alternative solutions includeeither reducing the amounts of such additives or carefully managing the balanceof positively and negatively charged additives to improve theof all of the polymeric materials on fiber surfaces.Some other measures thatcan be considered to reduce various possible root causes of foam include repairof pump seals, repair and adjustment of pulp-washing equipment, and use of foam-controlagents and channel-blocking polymers to improve displacement efficiency duringpulp washing operations. Bubbles coming out of the headbox sometimes can bereduced by decreasing the level of turbulence in the headbox, adjusting theto minimize splashing,and adjusting to prevent excessiveaction on a.Increased problems withdissolved and entrained air (in addition to some deposit problems) usually canbe expected if furnish that contains is exposed to acidic conditions below avalue of about 6.5. Just as in the case of ant-acid tablets, the reaction betweencalcium carbonate and acid leads to the release of carbon dioxide gas.
The highsolubility of CO 2 means that a high proportion will tendto remain dissolved in the water. Some of this elevated level of dissolved airwill tend to come out of solution as entrained air when the jet of furnish emergesfrom the, greatly lowering thepressure. The tiny bubbles can act just like fiber fines in impedingfrom the stock.ReferencesAvery-Edwards, D.
J., Elms,R., and Buckingham, A., 'Silicone Antifoams for Nonwoven Applications,'Tappi J. 77 (8): 35 (1994).Helle, T.
Lingo 14 0 keygen torrent. ABBYY Lingvo x. 6 Professional 1. ABBYY Tutor Grammar -. LINGO all versions serial number and keygen. LINGO 8.0 Serial Number Keygen for All Versions. Lingo 14.0 Serial Number Serial Numbers. Convert Lingo 14.0 Serial Number trail version to full software. Title: Lingo 14.0 Crack Size: 4.7 MB Launch settings and lingo 14.0 crack under system, tap lock screen. Toshiba will probably want to possess a memory. LINGO 14.0 Full Download, LINGO 14.0 Cracks, LINGO 14.0 Serials, LINGO 14.0 Keygens. Lingo 14.0 COMFAR III Expert v3.0. Keygen, free, torrent. LINGO also comes with dozens of real- world based examples for you to modify and expand.
K., Meinander,P. O., Nykanen, R. J., Molander, K. S., and Paulapuro, H.
V., 'Air RemovalMill Trials Using Pomp Deaerator,' TAPPI J. 82 (6): 146 (1999).Lorz, R. H., 'Air Content,Retention, and Drainage: Important Parameters in Paper/Board Production,'Pulp Paper Can. 88 (10): T361 (1987).Matula, J., and Kukkamaki,E., 'How to Deal with Difficult Passengers,' Pulp Paper Europe 1 (10):121 (1997).Matula, J. P., and Kukkamaki,E., 'New Findings of Entrained Air and Dissolved Gases in PM Wet End: MillCase Study,' TAPPI J 83 (4) no page (2000).May, O.
Entrained Air Measurement
W., and Buckman,S. J., 'Practical Effects of Air in Papermaking,' Tappi 58 (2): 90(1975).Rauch, R., and Sangl, R.,'Latest Findings on Entrained Air and Dissolved Gases in Pulp Suspensions,'Proc.
Entrained Gas Tester
TAPPI 2000 Papermakers Conf., 159 (2000).Wortley, B., 'Choosing the Right Weapon in the War on Foam,' PIMAMag. 71 (3): 36 (1989).PLEASE NOTE: Theinformation in this Guide is provided as a public service by Dr. Hubbe of the Department of Wood and Paper Science at North Carolina StateUniversity (mhubbe@ncsu.edu). Users of the information contained on these pagesassume complete responsibility to make sure that their practices are safe anddo not infringe upon an existing patent. There has been no attempt here to givefull safety instructions or to make note of all relevant patents governing theuse of additives. Please send corrections if you find errors or points thatneed better clarification.